介紹了華能某發電公司新建超超臨界660MW機組煙道(主煙道和旁路煙道)蒸發結晶脫硫廢水零排放技術的工藝流程、控製策略,調試期間現場試驗研究了投運該零排放技術前後,空氣預熱器(空預器)參數、一級省煤器後給水溫度、低溫省煤器參數和機組主參數的變化,分析了該脫硫廢水零排放係統對電除塵、脫硫水耗、輸灰流動性和灰品質的影響。
結果表明:該煙道蒸發結晶脫硫廢水零排放技術對一級省煤器後給水溫度、熱一、二次風溫、空預器出口排煙溫度和灰品質均有一定影響,但影響較小;有利於提高電除塵效率,煙道蒸發結晶脫硫廢水零排放技術安全、節能、高效,具有推廣應用價值。
石灰石-石膏濕法煙氣脫硫技術,因其具有煤種適用範圍廣、脫硫效率高、反應速度快、運行成本低等優點,被國內燃煤電站普遍采用。在濕法脫硫洗滌煙氣的過程中,煙氣中的飛灰會進入石膏漿液內,其中所含氯離子、重金屬離子等有害物質也隨之進入到煙氣脫硫係統中,並在石膏處理工藝過程中隨著衝洗水進入脫硫廢水環節,形成了富含重金屬和氯離子的脫硫廢水。
為了維持脫硫裝置漿液循環係統的物質平衡,防止脫硫設備被腐蝕,保證石膏質量,必須從脫硫係統中排放一定量的廢水。燃煤電站脫硫廢水存在總量少、汙染物含量大、易產生二次汙染等問題,故采用煙道(主煙道和旁路煙道)蒸發結晶的方式實現煙氣脫硫廢水零排放,具有重大的現實意義。
煙道蒸發結晶廢水零排放技術因其成本較低、占地麵積小、維護費用低等優點被國內專家學者廣泛研究。國內外學者通過建模計算分析得出:彎曲煙道可使液滴在煙道中停留的時間更長;為確保液滴在進入除塵器前完全蒸發,同時考慮蒸發效果、能耗成本和實際條件,建議工程應用中將霧化液滴直徑控製在60μm,煙溫控製約為130 ℃。
基於上述理論研究,華能某發電公司將煙道蒸發結晶廢水零排放技術應用於新建超超臨界 2×660MW機組,該機組由西安熱工研究院有限公司負責調試。
1 係統介紹
該機組采用煙道蒸發結晶廢水零排放技術,在主煙道和旁路煙道均布置了脫硫廢水噴霧裝置(空氣霧化噴嘴)。圖 1 為該工程方案的整體示意。
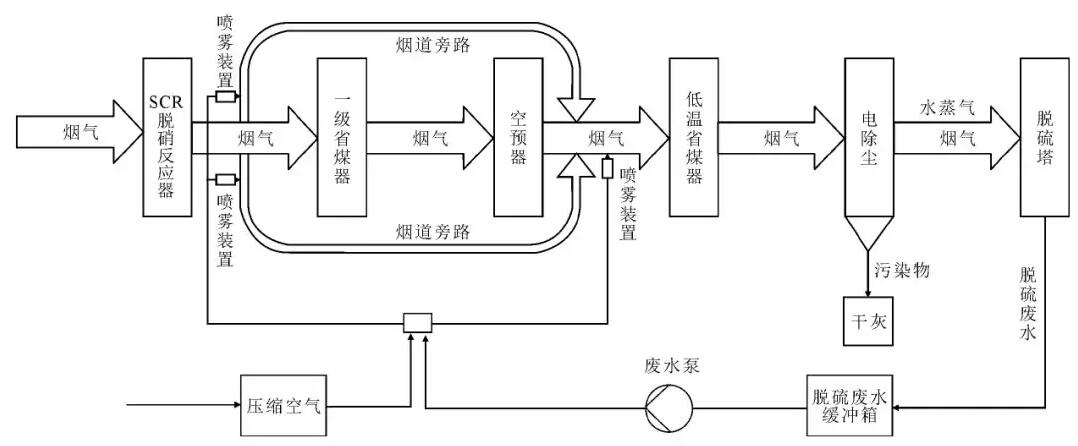
由圖 1 可見:空氣預熱器(空預器)出口至低溫省煤器為主煙道,主煙道噴霧裝置分布於空預器出口的豎直煙道內,且置於同一截麵的煙道兩側;旁路煙道在選擇性催化還原(SCR)脫硝反應器出口煙道有4個取煙口,每2個取煙口匯到1個旁路煙道中,旁路煙道內布置有噴霧裝置,2段旁路蒸發煙道再分別匯到空預器出口的水平主煙道中。
脫硫廢水在鋼製緩衝箱內沉澱後,由廢水泵打入若幹個廢水霧化裝置中,廢水與壓縮空氣在霧化裝置中混合形成直徑小於60μm 的霧滴,再經噴嘴噴入高溫煙氣中迅速蒸發結晶。脫硫廢水霧滴中含有的重金屬等汙染物轉化為結晶物或鹽類等固體,隨煙氣中的飛灰一起被電除塵器收集下來。
脫硫廢水緩衝箱內的沉澱物經壓濾機處理後外運,蒸發的水蒸氣則重新進入脫硫係統,從而實現了廢水零排放。該係統可實現噴入霧滴壓力、流量的自動調節。好文推薦:中水回用處理技術的特點!
圖 1 脫硫廢水零排放係統示意
脫硫廢水經高度霧化後噴入煙道內,絕大部分液滴微粒在煙氣的拖拽作用下,與煙氣流動保持一致。極少數液滴微粒因布朗運動在煙道內自由擴散,並吸附了煙氣中的灰份擴散到煙道壁上,高溫下液滴微粒中水份瞬間蒸幹,灰份黏結在煙道壁上,經過長期運行灰份逐漸累積加厚,形成積灰。在設計脫硫廢水零排放係統時,通過計算流體動力學(CFD)模擬分析,確定微粒擴散至煙道壁的位置和分布規律,在運行期間利用吹灰蒸汽定時自動多點位吹掃煙道,及時掃清煙道壁灰份,避免煙道內部積灰。吹灰器根據脫硫廢水蒸發的煙道結構,設計為多層交叉形式,采用回轉式伸縮結構,確保吹掃麵積達到 95%以上,同時對灰分易黏結的煙道壁板進行防腐處理。
該脫硫廢水零排放係統采用集中控製,通過采集分布在煙道內多部位的傳感器信號,將機組負荷、煙氣流量和排煙溫度等數據傳入數據處理及運算單元進行綜合分析,從而獨立控製各廢水霧化裝置的噴霧量,最大限度地利用煙氣熱量蒸發廢水。同時,設置專用保護模塊,在機組負荷低、煙氣流量小和排煙溫度低等蒸發條件欠佳的工況時,霧化裝置減少或停止噴霧,確保該係統不對機組運行造成任何不利影響。
另外,該脫硫廢水零排放係統為防止脫硫廢水中的雜質造成係統管路的汙染和堵塞,還配備了清水自動衝洗和狀態監控設備,可實現整條廢水管路和沿程設備的定期清水自動衝洗,衝洗裝置的衝洗流量、壓力可自動調節。